With the help of Callaghan Innovation's Manufacturing Robots Trials, Kiwi companies are integrating 'cobots' alongside their staff to gain efficiencies and stay competitive.
At a glance
- Robotics allows Kiwi manufacturers to compete with lower-cost producers, the ‘cobots’ working alongside staff and helping to eliminate boring, repetitive tasks.
- Using Callaghan Innovations Manufacturing Robots Trial, companies like Air New Zealand and Assa Abloy have been able to test and learn using the UR5 robot without the upfront expense. Assa
- Assa Abloy saw return on investment on the UR5 robot is around 12 months, with Air New Zealand also able to prove the concept as a viable one for the airline.
"By removing this barrier, Callaghan Innovation enabled us to investigate what did and didn’t work and we were able to make our mistakes early and learn from them.”
Wayne Thomas, 3D Printing and Advanced Manufacturing Project Manager, Air New Zealand
No more repetition, all automation
Robots. They’re no longer the thing of movies, or a futuristic novelty. They’re being used in the manufacturing industry especially to help eliminate repetitive, boring tasks, and ultimately, through increased automation, achieve cost savings for businesses.
But naturally there is some hesitation amongst employees that robots will replace their jobs. In fact, the cobots are taking away the heavily repetitive tasks and leaving the employees available to participate in higher-value tasks.
Callaghan Innovation’s Phil Anderson, Business Innovation Advisor for Manufacturing and Niche, says the initial resistance to robots often disappears when employees realise the ‘cobots’ complement the human workforce and can be used to reduce monotonous or risky tasks.
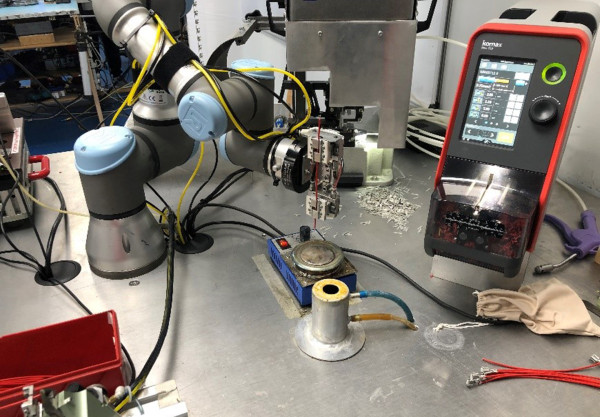
Wire work: ‘Rosie the Robot’ is currently tasked with making 10,000 little wires via a repetitive, fully automated seven-step process.
Trialling and testing robotics with Callaghan Innovation
Deploying robots in manufacturing can come with heavy investment of time and capital, but with Callaghan Innovation’s Manufacturing Robots Trials, two major Kiwi companies have been able to test high-capacity UR5 robots for a one month period.
Assa Abloy, door and window lock and hardware maker, compared the UR5 to Callaghan Innovation’s ‘Baxter’ robot in 2016, later deploying the UR5 into its production line. This helped the business achieve better consistency of product and more efficiently achieve its goal of producing any key or lock in any colour with a two-day turnaround.
Air New Zealand also took advantage of our UR5 trial in 2018 to see how the robotic arm could help it gain efficiencies also, using it to automate its sandblasting process.
Air New Zealand's 3D Printing and Advanced Manufacturing Project Manager, Wayne Thomas, says "It is difficult to justify the expense of sourcing a robotic arm for a short period of time when success is not guaranteed."
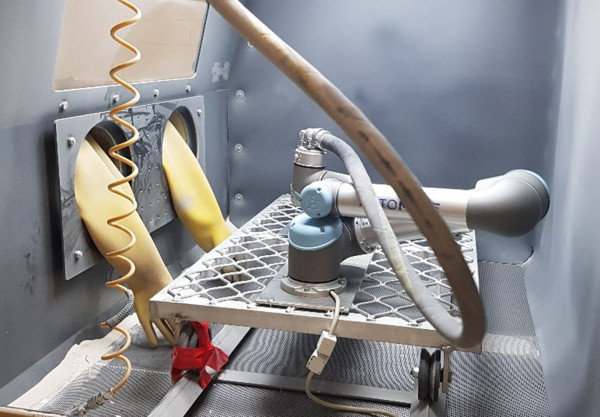
Air New Zealand was able to trial a UR5 robotic arm as a tool to automate its sandblasting process.
"By removing this barrier, Callaghan Innovation enabled us to investigate what did and didn’t work and we were able to make our mistakes early and learn from them.”
The value of a helping hand
After integration, Assa Abloy has calculated that they have seen a return on investment, in terms of the UR5 paying for itself, in approximately 12 months.
And for Air New Zealand, as a result of the trial Thomas says they have been able to prove the concept is viable for the airline.
“We now know the robotic arm could work for the business but we didn’t have the risk of wasted expenditure that would have come from buying and experimenting with our own robotic arm only to find it wasn’t a good fit,” he says.